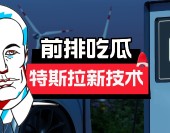
繼上個專欄,我們介紹了特斯拉最新的技術。衆所周知,進入2023年後,特斯拉就开始接連降價,讓利於客戶,發力中端市場,衝擊國產車。那么它降價背後得益於什么呢?是技術還是管理?
極致制造,決勝成本
特斯拉始終堅持將降本理念貫穿至企業生產、經營等各個環節,自2018年以來,實現Model 3整車降本30%,同時,下一代汽車平台目標實現降本50%。爲實現這一目標,特斯拉外部注重簡化供應鏈體系,構建本土化生產模式;內部注重精細化管理+產品迭代升級,一體化壓鑄+4680CTC定義極致制造,引領產業變革浪潮。
供應鏈簡化+本土化生產,強化區域供需平衡。特斯拉在全球三大市場分別設有超級工廠,通過在原有供應鏈基礎上,簡化Tier1和Tier2,加深垂直整合,實現95%以上的供應鏈本土化(以上海工廠爲例),保障區域供需平衡。
一體化壓鑄+4680CTC定義極致制造。一體化壓鑄顛覆衝壓&焊裝,4680 CTC提升總裝效率。前、後地板一體化壓鑄+4680 CTC+四門兩蓋、側圍,同時並行塗裝、總裝流程,裝配效率提升44%,空間效率提升30%,下一代平台成本有望下降50%。
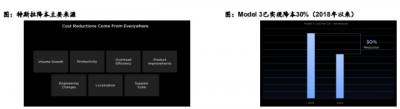

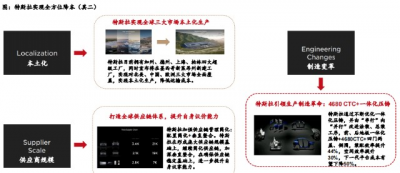
特斯拉全新動力系統預計可實現降本1000美元。在下一代全新動力總成中,特斯拉在保證整車性能和效率不變的情況下,計劃減少75%的碳化硅使用量,永磁電機不再使用稀土材料。此外,全新動力系統可實現與任何電池化學物質的兼容,極大地提升了電池制造的靈活性和種類來源,預計全新動力系統將可實現降本1000美元/輛。
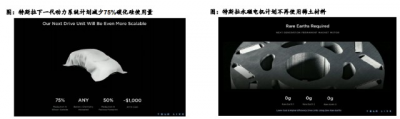
一體化壓鑄:开啓9000噸級壓鑄機時代
9000噸級壓鑄機Giga Press完成交付,未來將用於Cybertruck車身生產。2022年5月特斯拉向意德拉採購9000TGiga Press超大型壓鑄機,並計劃用於Cybertruck車身一體化壓鑄當中。2022年10月,意德拉宣布用於Cybertruck車身制造的9000T壓鑄機GigaPress已完成建造和測試,並於2022年末在德州工廠完成組裝。此外,2022年12月,新一批66台庫卡機器人已抵達德州工廠,預計未來將配合Giga Press共同應用於Cybertruck生產线當中。
截至目前,特斯拉向意德拉採購的3台9000T超大型壓鑄機已全部抵達德州工廠。根據特斯拉投資者日消息,Cybertruck將在年內正式發布。我們預計,2023年年中將進入小批量生產階段,年底有望實現大規模量產。
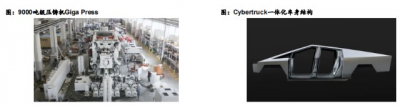
一體化壓鑄:前、後地板全面應用,整體焊點減少1600+個
特斯拉一體化壓鑄全面拓展至前地板。Model Y一體化壓鑄後地板總成,整體零件數量將由70個減少至1-2個,預計減少焊點數量700-800個,目標實現下車體總成減重30%,制造成本下降40%;德州奧斯汀工廠生產的一體化壓鑄車身方案,可將前&後地板零部件數量從171減少至2個,焊接點數量減少超1600個。
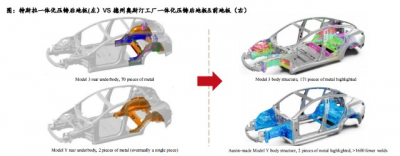
一體化壓鑄:四大超級工廠加速部署大型壓鑄機
特斯拉四大工廠加速部署大型壓鑄機,對應一體化壓鑄年產能約爲150萬件。目前,特斯拉四大工廠共計部署15台以上大型壓鑄機,其中上海工廠在裝配5台大型壓鑄機,用於Model Y後地板生產的基礎上,繼續加速部署更多大型壓鑄機。德州工廠引入9000T Giga Press超大型壓鑄機,並計劃用於Cybertruck車身一體化壓鑄,开啓9000噸級壓鑄機時代。特斯拉四大工廠對應一體化壓鑄年產能已達到150萬件左右。
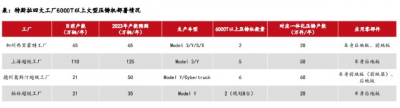
一體化壓鑄VS傳統工藝:簡化生產工序,降低人工成本
傳統壓鑄工藝:以生產下車體總成的流程爲例,整車廠以卷鋼爲最初輸入,經衝壓、焊接工序完成前、中、後地板總成,最後通過一定數量的連接件進行組裝,得到下車體總成。
一體化壓鑄工藝:該工藝大幅度減少衝壓、焊接使用量,一體化地板直接通過超大型壓鑄機壓鑄成型,再通過少量連接件進行組裝,將原有9道降低至2道,效率得到顯著提升。
一體化壓鑄實現工藝簡化,將大幅減少人工成本。據智駕網和愛卡汽車,北京現代順義工廠年產能45萬輛,其車身車間員工爲218人。我們測算,傳統衝壓&焊接工藝需要工人約120人,而一體化壓鑄工藝僅需要約30人,人工成本大幅減少。
一體化壓鑄VS傳統工藝:零件數量大幅減少,生產效率快速提升
一體化壓鑄可將下車體總成(前中後地板總成)零部件數量減少至2-3個。仍以下車體總成爲例,使用傳統衝壓&焊接工藝需要超370個零件,一體化壓鑄則直接輸出下車體總成2-3個,再經少量焊接後,即可完成下車體總成的制造。
一體化壓鑄可顯著減少工時、實現躍進式提效。傳統工藝下,下車體總成制造將經過衝壓、焊接兩大車間,總工時超2小時。相比之下,特斯拉Model Y後地板壓鑄時間已縮短至120秒,預計日產能將超過400件,生產效率提升約40倍。
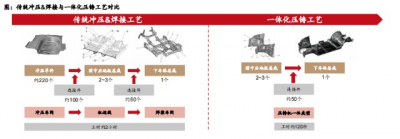
一體化壓鑄VS傳統工藝:大幅降低焊點數量,降本作用明顯
整車上的連接點數量一般在3000-6000個之間。以奧迪A8爲例,新一代奧迪A8車身上大量應用了自切削螺釘聯接、激光焊接、鉚接等技術,車身連接工藝達到了14種,包括MIG焊、點焊、保護焊、遠程激光焊等8種熱連接技術和專門針對鋁材的衝鉚連接、用於不同材料拼接的自攻螺栓、卷邊連接等6種冷連接技術,連接點數量預計超5000個。
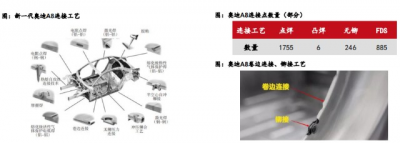
一體化壓鑄VS傳統工藝:壓鑄機等設備成本下降
傳統衝壓工藝制造設備主要爲壓力機、衝壓模具。在衝壓環節分爲整車廠採購的外覆蓋件壓力機和零部件廠採購的車身結構件組件壓力機。二者通過更換不同的衝壓模具可實現多種外觀尺寸衝壓件生產。
預計50萬產能的生產线需要衝壓設備投資約1億元。根據《大型汽車衝壓生產线技術與裝備現狀與發展》等文章顯示,我們測算衝壓制造車身前、後地板的過程約分別需要:大型壓力機1台,小型壓力機15台。大型衝壓模具1台,小型衝壓模具15台,設備總成本約1億元。
預計50萬產能的生產线需要焊接設備投資約爲1.25億元。參考《東風本田二工廠10萬台車身柔性焊裝线工藝設計和應用》和汽車公社相關文章,我們測算傳統工藝下生產Model Y後地板焊點所需數量700-800個,前地板焊點所需數量900-1000個,生產所需的焊接設備投入約1.25億元。
預計年產能50萬台的生產线需要布局5套6000T以上壓鑄島,成本約爲2.5億元。壓鑄島的基本外圍設備有熔煉爐、噴塗設備、拾取設備、空氣冷卻架貨水冷箱、修邊機、氣缸內襯輸送帶、模具溫度機等,與壓鑄機、壓鑄模具等核心設備組合在一起即構成壓鑄生產單元,即壓鑄島。考慮到下車體大型結構件至少需要6000T以上的壓鑄機,我們測算,年產能50萬台的生產线需要爲下車體總成布局預計5套6000T以上壓鑄島,成本約爲2.5億元。
一體化壓鑄VS傳統工藝:前、後地板將分別實現降本489/307元/輛
一體化壓鑄後地板預計可實現降本307元/輛。我們通過對傳統工藝和一體化壓鑄工藝生產車身地板所用的設備、人員、制造、原材料等成本進行核算,以年產能50萬輛的產线爲例,假定傳統/一體化壓鑄工藝良率分別爲95%/90%,同時考慮10年期的設備折舊。經測算,預計一體化壓鑄後地板單車可實現降本307元。
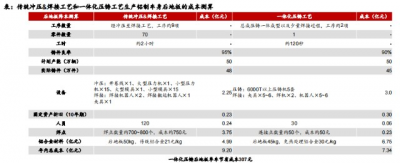
一體化壓鑄前地板預計可實現降本489元/輛,合計實現降本796元/輛。參照後地板定量降本的測算方式,預計前地板可實現單車降本489元,前、後地板合計實現降本796元/輛。此外,考慮到整車重量的下降對續航裏程的提升效果,同等續航裏程要求下,單車電池成本將會下降。我們預計,隨着一體化壓鑄應用拓展,中長期降本將有更大空間。
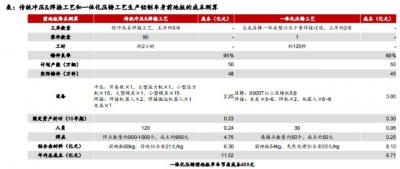
投資建議和盈利預測
宏圖第三篇章开啓,特斯拉生產制造革命加速。
特斯拉產業鏈經歷三個階段:上海工廠开啓“特斯拉浪潮”,疫情後“特斯拉加速向中國工廠轉變”,當前正在進入“墨西哥工廠加速向國產供應商轉變”。
投資建議:
供應鏈變革 asp 持續增長,帶動特斯拉產業鏈供應商全面突破歷史收入天花板,加速墨西哥建廠,在墨西哥开啓第二輪國產替代,並有望成長成爲國際 Tier1, 建議關注重點公司拓普集團,旭升集團,新泉股份,銀輪股份。
特斯拉生產制造革命:一體化壓鑄+4680 CTC。1)大噸位壓鑄機,建議關注力勁科技、伊之密;2)模具、免熱材料,建議關注合力科技、永茂泰、立中集團;3)壓鑄件,建議關注愛柯迪、文燦股份、廣東鴻圖;4)4680CTC,建議關注三花智控。
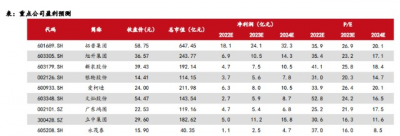
風險提示:
一體化壓鑄技術應用拓展不及預期。大型壓鑄機產能爬坡進展受阻,導致設備的延期交付,將直接影響下遊主機廠一體化壓鑄結構件產品的量產進度低於預期。
特斯拉柏林工廠、德州工廠產能爬坡不及預期。目前,特斯拉四大工廠均已部署6000T以上大型壓鑄機,其中,德州工廠、柏林工廠產能仍處在爬坡階段。若兩大工廠產能爬坡不及預期,將直接影響到特斯拉銷量及一體化壓鑄結構件產品量產進度。
4680電池產量提升不及預期。特斯拉2023年推出的Cybertruck、Semi等新車型均只使用4680電池,預計全年需求量將超過10GWh,加州工廠、德州工廠的4680電池產量快速提升仍是關鍵,同時內華達州工廠的4680電池新工廠建設也將成爲中長期產能的重要保障。
重點關注公司業績不及預期。一體化壓鑄業務前期需要較大的資金投入,同時收益兌現需要經歷較長時間。若重點關注公司業績情況不及預期,將直接影響公司一體化壓鑄的進展。
上遊原材料價格波動。目前,鋁錠價格較去年已出現明顯回落,未來若鋁錠價格出現大幅反彈,將使得中下遊成本負擔加重,影響產業鏈平穩發展。
免責聲明:卓戴資本僅作爲行業信息及新聞分享,不代表支持或贊同本文觀點,若有任何異議或侵權,敬請聯系,我們會及時處理,謝謝!
本文作者可以追加內容哦 !
鄭重聲明:本文版權歸原作者所有,轉載文章僅為傳播信息之目的,不構成任何投資建議,如有侵權行為,請第一時間聯絡我們修改或刪除,多謝。
標題:第二彈,新篇章下特斯拉是如何降本的(下)?
地址:https://www.breakthing.com/post/54275.html